Understanding Elastomeric Core Options for Encapsulated O-Rings
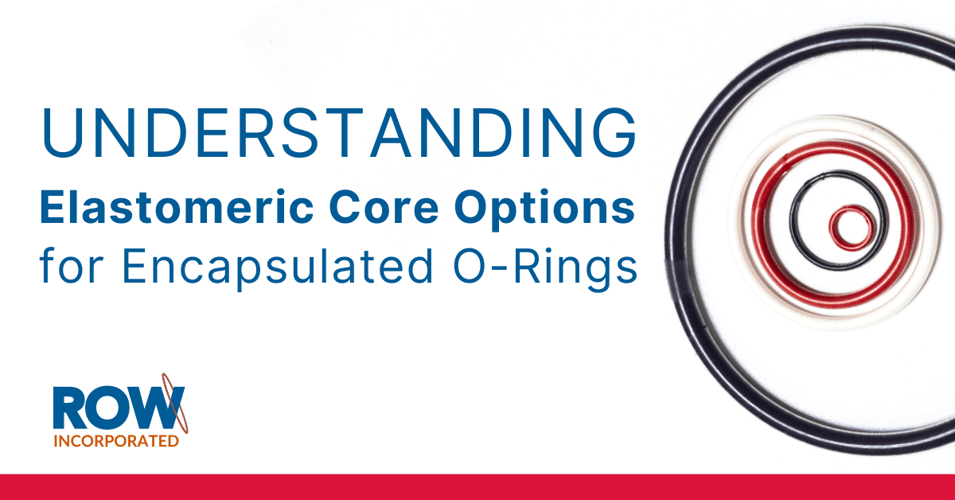
Table of Contents
Introduction:
Encapsulated O-rings are critical components in various industries, providing sealing solutions in demanding environments. One key aspect of these O-rings is the elastomeric core material, which plays a vital role in their performance. In this blog post, we delve into the technical specifications and characteristics of elastomeric core options to help you make informed decisions for your sealing applications.
Elastomeric Core Options:
Elastomeric cores serve as the backbone of encapsulated O-rings, providing the necessary resilience, flexibility, and sealing properties demanded by a wide range of applications. Understanding the diverse options available is crucial for tailoring solutions to specific operational requirements. Let's delve deeper into each elastomeric core option:
-
Solid Silicone: Solid silicone cores offer a robust sealing solution with exceptional temperature resistance and moderate solvent resistance. Their solid structure ensures uniform performance and reliable sealing even in demanding conditions. With compliance to A-A-59588 (formerly ZZ-R-765) 70 durometer FDA standards, solid silicone cores are favored for applications where stability and durability are paramount.
-
Hollow Silicone: Hollow silicone cores combine flexibility with resilience, making them ideal for dynamic sealing applications. Compliant with A-A-59588 70 durometer FDA standards, these cores exhibit low compression set and excellent recovery properties, ensuring prolonged service life even under repeated cycles of compression and decompression.
- FKM (Viton™): Renowned for its exceptional heat resistance and chemical compatibility, FKM cores offer unparalleled performance in extreme environments. Meeting AMS 3216 standards (formerly MIL-R-83248C), FKM cores excel in applications where exposure to high temperatures, aggressive chemicals, and harsh operating conditions is common. Their low compression set at elevated temperatures ensures reliable sealing under thermal stress.
-
EPDM: EPDM cores provide a versatile sealing solution with excellent weather aging resistance and broad chemical compatibility. FDA compliant and capable of withstanding temperatures ranging from -65° to +300°F (-54° to +150°C), EPDM cores are well-suited for applications exposed to outdoor elements, steam, water, and a wide range of organic and inorganic acids.
Temperature Ranges and Chemical Compatibility:
Understanding the temperature limitations of encapsulated O-rings is crucial for selecting the right combination of elastomeric core and encapsulation material. FEP and PFA encapsulation offer exceptional temperature resistance, with PFA in particular reaching up to 500°F (260°C). When paired with appropriate elastomeric cores, these encapsulated O-rings can withstand a wide range of operating temperatures and harsh environmental conditions.
While FEP and PFA exhibit excellent chemical inertness, some chemicals may permeate the encapsulation through years of exposure, which may affect the integrity of the elastomeric core. Careful consideration should be given to selecting a core material that is most compatible with the chemicals present in the application environment, minimizing the risk of degradation and ensuring reliable sealing performance.
By evaluating the temperature requirements and chemical exposure of your specific application, you can make informed decisions regarding the selection of elastomeric core and encapsulation material. This proactive approach will help mitigate potential risks and ensure the longevity and effectiveness of encapsulated O-rings in demanding operating conditions.
Characteristics of Encapsulated O-Ring Core Material:
-
EPDM: Withstanding temperatures from -65° to +300°F (-54° to +150°C), EPDM cores exhibit excellent resistance to weather, steam, and various chemicals.
-
Silicone: Operating within a range of -67° to +500°F (-55° to +260°C), silicone cores offer low compression set, heat resistance, and ozone aging resistance.
-
FKM (Viton™): FKM cores, enduring temperatures from -15° to +400°F (-26° to +205°C), demonstrate low compression set at elevated temperatures and resistance to ozone, weather, and aging.
Design Tips and Recommendations:
Selecting the appropriate elastomeric core and encapsulation material is a critical aspect of designing encapsulated O-rings for optimal performance and longevity. Here are some essential design tips and recommendations to consider:
-
Compatibility Assessment: Conduct a thorough assessment of the compatibility between the elastomeric core material, encapsulation material, and the operating environment. Consider factors such as chemical exposure, temperature variations, pressure fluctuations, and mechanical stresses to ensure compatibility and prevent material degradation over time.
- Chemical Resistance: Take into account the specific chemicals present in the application environment and their potential interactions with the elastomeric core and encapsulation material. Choose a core material that offers the highest resistance to the chemicals involved to minimize the risk of degradation and ensure long-term sealing effectiveness.
-
Temperature Considerations: Evaluate the temperature range of the application and select elastomeric core and encapsulation materials that can withstand the expected operating temperatures without compromising performance. Pay attention to temperature extremes, as well as temperature fluctuations, to ensure consistent sealing performance under varying conditions.
-
Mechanical Properties: Consider the mechanical properties of the elastomeric core, such as resilience, compression set, and tensile strength, to ensure reliable sealing under dynamic operating conditions. Choose a core material that can withstand repeated compression and decompression cycles without losing its sealing integrity.
-
Environmental Factors: Factor in environmental conditions such as exposure to UV radiation, ozone, moisture, and atmospheric pollutants. Select elastomeric core and encapsulation materials that offer excellent weather aging resistance and environmental durability to maintain sealing effectiveness over time.
-
Consultation and Testing: When in doubt, consult with material experts or conduct laboratory testing to evaluate the suitability of elastomeric core and encapsulation materials for your specific application. Test samples under simulated operating conditions to assess performance and identify any potential issues before full-scale implementation.
-
Monitoring and Maintenance: Establish a regular monitoring and maintenance schedule to inspect encapsulated O-rings for signs of wear, degradation, or failure. Implement preventive maintenance measures, such as periodic replacement or resealing, to ensure continued sealing effectiveness and prevent costly downtime or leakage incidents.
For more information on selecting the right elastomeric core and encapsulation materials for your encapsulated O-ring applications, feel free to contact us. Our team of experts is ready to provide personalized assistance and guidance tailored to your specific needs. Unlock the full potential of your sealing solutions with our expertise and support at ROW, Inc.