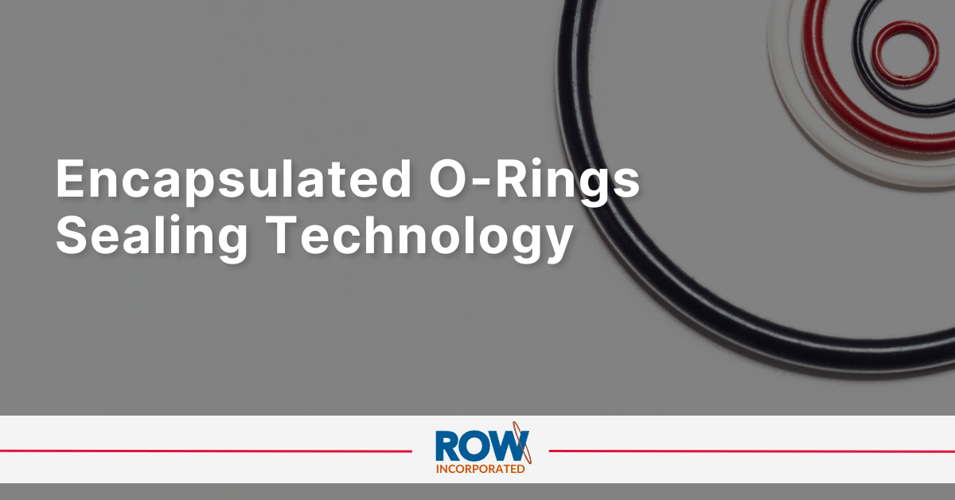
Table of Contents
Encapsulated O-rings have revolutionized sealing technology, offering resistance to harsh chemicals, extreme temperatures, and versatility.
What are Encapsulated O-Rings?
Encapsulated O-rings are designed to offer reliable sealing when exposure to harsh chemicals and extreme temperatures are a concern. They consist of an elastomeric core enclosed in a hard sheath, usually made of materials like FEP or PFA. These O-rings offer outstanding chemical resistance while maintaining compressive elasticity.
Their Purpose in Sealing Technology
Encapsulated O-rings combine the best features of elastomers and Teflon to achieve excellent chemical resistance while maintaining excellent longevity and low compression set. This hybrid provides compressive resilience, enhanced temperature resistance, reduced friction, and improved sealing performance. O-rings with FEP or PFA encapsulation are available with many elastomeric cores as well as steel spring energizers in the near future. They provide effective solutions for challenging applications, ensuring seal integrity even under aggressive conditions where a non-encapsulated O-ring may experience chemical attack.
Types of Encapsulated O-Rings
Teflon® Encapsulated O-Rings
Teflon® Encapsulated O-rings combine Teflon's chemical resistance with the properties of elastomers. ROW, Inc. offers two types of Teflon: FEP and PFA. The resulting product excels in sealing technology, offering unique advantages.
Notable features include:
- Superior Dielectric Properties: High electrical insulation offers improved device safety.
- Low Coefficient of Friction: Ensures reduced wear and prolonged lifespan.
- Flexibility and Toughness: Enables easy application in varied settings.
- Negligible Moisture Absorption: Protects the O-ring integrity against moisture-induced issues.
Teflon Encapsulated Silicone O-rings
Teflon Encapsulated Silicone O-rings have exceptional properties that enhance their utility in sealing technology. Some of these properties include:
- High Thermal Stability: This ensures consistent performance even under extreme temperatures. These can be encapsulated in PFA or FEP and PFA can go up to 500ºF (260ºC).
- Corrosion Resistance: Provides the capacity to withstand a remarkable variety of corrosive mediums.
- Compressive Resilience: Assures low compressive deformation and high recovery after deformation.
Teflon Encapsulated FKM (Viton®) O-Rings
Yet another significant variant in this range is the Teflon Encapsulated FKM O-Rings. Notably, these O-rings integrate some superb features that make them an effective solution across several industrial applications, such as:
- Superior Heat Resistance: Enables sustained performance under extreme heat conditions. ROW, Inc. offers FEP and PFA options with both options being able to handle 400ºF (205ºF).
- Outstanding Chemical Resistance: Ensures resistance against a broad spectrum of chemicals.
- Excellent Compression Set: Assures maximum sealing efficiency with the least deformation.
Teflon Encapsulated EPDM O-Rings
EPDM provides O-rings with a combination of weather resistance, flexibility, chemical resistance and sealing ability, making them suitable for a wide variety of applications in various industries. Some of the qualities that EPDM brings to O-rings include:
-
Excellent weather resistance: EPDM is highly resistant to the elements, including exposure to sun, rain, snow, and temperature fluctuations. This resistance makes it suitable for outdoor use.
-
Good Ozone Resistance: EPDM is known for its ability to resist degradation caused by exposure to atmospheric ozone, making it suitable for outdoor applications.
-
Good chemical resistance: EPDM is resistant to a wide variety of chemicals, including acids, alkalis and solvents. This makes it suitable for applications where O-rings may come into contact with corrosive chemicals.
Advantages of Encapsulated O-Rings
Enhanced Chemical Resistance
One of the biggest selling points is their unbeatable chemical resistance in hostile environments. They are designed to withstand a wide array of corrosive chemicals like alcohols, acidic solutions, or petroleum spirits. This makes them an ideal pick for industries dealing with challenging chemical applications where other seal types might fail. Compared to other seal types, Encapsulated O-Rings also offer higher mechanical strength, ensuring better durability and resistance to cracking and stress. The combination of these components creates an o-ring that is virtually chemically inert and compression set resistant, providing unique properties for a range of demanding applications, including use in harsh sealing environments.
Improved Temperature Range Performance
Another point to note is their ability to perform evenly over a wide temperature range - from extreme heat to severe cold environments. The performance stability of Encapsulated O-Rings across such varied conditions makes them a go-to solution in sectors where temperature variations are inevitable.
Reduced Friction & Wear
The low coefficient of friction of Encapsulated O-Rings can assist in installation and warrants lesser wear, thereby elongating the component lifespan. This low friction advantage not only underlies their durability but also reduces the total cost of ownership by decreasing the maintenance needs and replacement frequency.
Future Prospects for Encapsulated O-Rings in Sealing Technology
Encapsulated O-rings are a promising sealing technology due to their exceptional performance, adaptability, and application across various industries. They are critical components that provide powerful and effective sealing solutions. As businesses recognize the strategic value of these seals, industry experts anticipate increased adoption in the future. With advancements in materials, manufacturing, and testing methods, encapsulated O-rings, including piston seals, are continuously evolving to solve complex industrial challenges. One key advantage of encapsulated O-rings is their excellent resistance to almost all types of media, making them suitable for a wide range of applications, including metric sizes. In cryogenics, steel springs are being sought out to be encapsulated to ensure optimal sealing even at the most extreme temperatures. While encapsulation may have limitations, understanding these challenges helps harness their potential and mitigate risks in highly sensitive operations. As companies prioritize operational efficiency, the adoption of encapsulated O-rings is inevitable. These powerful components will continue to evolve and make significant strides in sealing technology. Encapsulated O-rings are generally best suited to static applications, or in slow moving rotary applications. Encapsulated O-rings bring forth unprecedented levels of chemical resistance, temperature resilience, and reduced friction or wear. Their impressive performance across varied harsh conditions significantly contributes to the advancement of sealing technology, pushing the envelope for what's achievable in sealing solutions in the future.