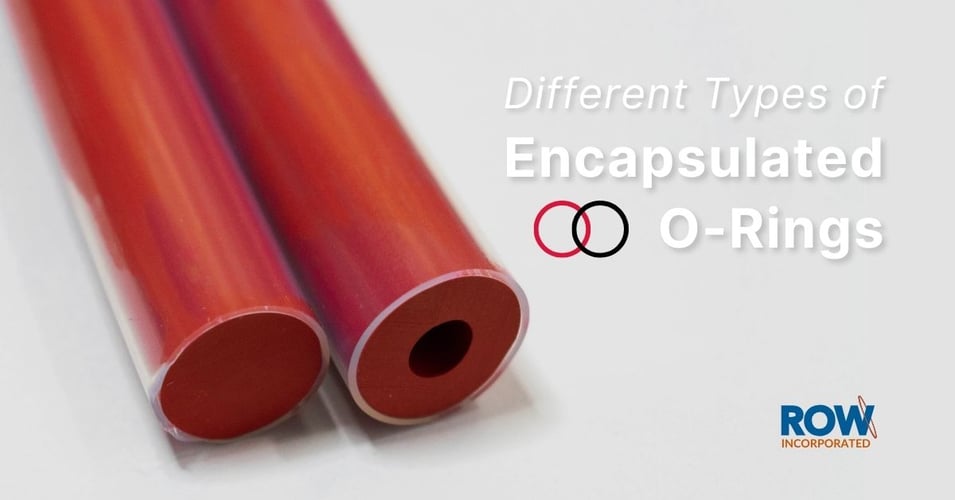
Table of Contents
Key Highlights
- Encapsulated O-rings blend the resilience of elastomers with the high chemical resistance and thermal stability of Teflon®.
- Two primary types of encapsulated O-rings include those with a solid core, typically made from silicone or FKM (Viton®), and those with a hollow core that offer extreme elasticity.
- The jacket types and O-ring cores are designed carefully to resist a wide array of corrosive chemicals and diverge over a broad spectrum of temperature ranges.
- The choice of solid or hollow-core design provided by encapsulated O-rings contribute significantly to their suitability across diverse applications.
- Although encapsulated O-rings prove to be excellent in many cases, they do have certain limitations, and it is vital to understand these before choosing an encapsulated O-ring suited for your needs.
Introduction
Today, industrial applications demand robust materials that can withstand significant pressure, aggressive chemicals, and a considerable range of temperatures. That's where encapsulated O-rings step in. Combining the chemical resistance of Teflon® and the elasticity of a silicone core, encapsulated O-rings are highly versatile seals that work even in the most challenging environments. This blog dives into the types of encapsulated O-rings along with their uses, advantages, and how they can be tailored to meet different requirements, offering unique benefits for various industries. Understanding the specifics of encapsulated O-rings can help you decide when and where they can be beneficial for your specific use case.
What are Encapsulated O-rings?
An encapsulated O-ring is a specially developed seal, designed to solve common problems across numerous industries. Combining the best of Teflon® and an elastomeric core, these O-rings bring flexibility and chemical resistance together - properties which may not generally co-exist in other types of seals.
The outer jacket of the encapsulated O-ring is made from Teflon®. Teflon®, as many may know, possesses high thermal stability and resistance to corrosion, making it ideal for environments faced with aggressive chemicals and varying temperatures. The inner core, on the other hand, is made of rubber, often silicone or Viton®, which provides the needed compressibility and elasticity to create an effective seal.
These O-rings have two primary types of cores: solid and hollow. A solid core O-ring typically is made from silicone or FKM (Viton®). These offer excellent elasticity and a good compression set, making them suited for an extensive range of applications. Hollow core O-rings are designed for applications that require extreme elasticity. Although they might come with a slight compromise in terms of compression set and recovery, their flexibility often makes up for it.
For some applications EPDM materials are used in the manufacture of encapsulated O-rings to provide flexibility and effective sealing, while encapsulation is used to improve their resistance to adverse conditions. Both play an important role in sealing applications in a variety of industries.
All in all, encapsulated O-rings beautifully marry chemical resistance with the necessary flexibility, resulting in seals that successfully withstand challenging environments while delivering optimal performance.
Types of Encapsulated O-Ring Materials
Apart from choosing the right encapsulation material, encapsulated O-rings can be crafted in four distinct combinations of jacket types and elastomer cores. Let's explore each one in detail:
- Teflon® FEP encapsulating an FKM core (RFV) lets the FEP jacket provide resistance against various corrosive substances while the FKM core offers excellent resilience and a good compression set.
- Teflon® FEP encapsulating a Silicone core (RFS) mirrors the function of RFV O-rings as FEP offers chemical resistance while silicone core provides flexibility and heat resistance.
- Teflon® PFA encapsulating an FKM core (RPV) combines the thermal stability and durability of PFA with the resilience and high temperature tolerance of FKM.
- Teflon® PFA encapsulating a Silicone core (RPS) merges PFA's high temperature resistance and mechanical strength with the elasticity of silicone for extreme temperature applications.
- Teflon® FEP encapsulating an EPDM core (RFE) provides O-rings with a combination of weather resistance, flexibility, chemical resistance and sealing ability, making them suitable for a wide variety of applications.
- Teflon® PFA encapsulating an EPDM core (RPE) functions much like the RFE but with higher mechanical durability of the jacket.
These different types of encapsulated O-rings have been engineered to function optimally in varying environments. Depending on your application's specific needs regarding compressibility, elasticity, thermal stability, or resistance to corrosive substances, you can choose the appropriate combination of jacket and core materials.
Solid or Hollow-Core Design
The core design of encapsulated O-rings is one of their most defining features. The two offerings include solid and hollow-core designs—each bringing its strengths to the table.
Solid-core encapsulated O-rings mainly comprise a silicone or FKM elastomer core. With their robust design, these O-rings offer excellent resistance to compression set and recovery when released from being under load. This makes them the preferred choice for many demanding applications where superior resilience is critical.
On the other hand, hollow-core design encapsulated O-rings contain a circular gap, exhibiting greater flexibility. These O-rings are easier to squeeze, making them ideal for applications requiring a more pliable and less force-demanding seal.
Still, whether a solid or a hollow-core design would work best depends on the specific conditions of your application. In essence, the key lies in understanding the demands of your application and matching it with the correct encapsulated O-ring design.
Applications and Uses of Encapsulated O-rings
With their unique combination of chemical resistance, thermal stability, and adaptability, encapsulated O-rings find usage across numerous industries. Let's discuss some common applications:
In a Chemical & Petrochemical Context: Given their excellent resistance to aggressive chemicals, encapsulated O-rings are widely employed in industries dealing with chemical and petrochemical processes. They can efficiently withstand the harshness of various chemicals, providing a reliable sealing solution.
For Food and Drugs Processing: Encapsulated O-rings manufactured from FDA-approved materials ensure hygiene and safety in food and drug processing applications. Their non-contaminating material makes them ideal for use where cleanliness is paramount and resistance to certain types of cleaning chemicals are critical to the application.
In Cryogenic Equipment: Certain variants like steel spring core encapsulated O-rings are used for cryogenic sealing applications down to temperatures as low as -420°F.
Other Applications: Apart from the above, encapsulated O-rings are also found in valves, pumps, flanges, turbo pumps, turbo expanders, swivels, joints, and other applications that require enduring seals.
It's important to note that the success of an encapsulated O-ring greatly depends upon choosing the right product for the job. Understanding the nuances of your specific application can help you select the appropriate size, design, encapsulation material, and type of elastomeric core.
Limitations of Encapsulated O-rings
While encapsulated O-rings demonstrate impressive advantages, they do have certain limitations. For instance, their relatively thin outer jacket can make them susceptible to scratching, particularly in applications involving abrasive slurries or powders. In such scenarios, they may not be the most suitable option.
Highly dynamic systems are another application where encapsulated O-rings may not be recommended. They are generally better suited to static applications or those with slow-moving rotary components. Improperly chosen or installed encapsulated O-rings might showcase inadequate performance, underlining the importance of selecting the correct O-ring for your task.
In spite of these limitations, encapsulated O-rings continue to be a preferred choice owing to their versatile applicability in demanding environments and tasks. They supersede many conventional options, but understanding their shortcomings and working around them can ensure optimal results.
Conclusion
Summarizing, encapsulated O-rings deliver the winning combination of high chemical resistance, temperature stability, and the much-needed elasticity to create seals that effectively address common industrial challenges. Their design variations and the choices in encapsulation materials and cores pave the way for tailoring them to meet diverse application needs. While they might have certain limitations, understanding these before choosing an O-ring can pack on appreciable benefits. With the information outlined in this blog, you are now armed with the knowledge necessary to make an informed decision about using encapsulated O-rings in your industry.
Frequently Asked Questions
Are Teflon® Encapsulated O-rings Superior to Other Types?
Teflon® encapsulated O-rings incorporate the high chemical resistance of Teflon® and the elasticity of traditional elastomers, making them ideal for chemically hostile environments over a wide temperature range. Their specific superiority, however, would depend on the nature of your application.
What Sizes Do Encapsulated O-rings Come In?
Encapsulated O-rings come in a host of standard sizes, encompassing AS/BS/JIS standard diameters. They can also be crafted to non-standard metric or inch sizes based on specific specifications, catering to a broad spectrum of requirements.
How Do I Install an Encapsulated O-ring Properly?
Proper installation is critical for the performance of encapsulated O-rings. Here are a few steps:
- Ensure that the installation surfaces are free from sharp edges
- Refrain from excessive stretching or twisting during installation
- If this is installed over a shaft, you may heat the O-rings before installing them (boiling for 3 minutes is recommended)
- It helps to install the O-rings while they are still warm
How Long Do Encapsulated O-rings Last?
The service life of encapsulated O-rings largely depends on their application, specific type, and the environment in which they are used. Proper installation and ensuring that the selected O-ring fits the demands of the application can potentially increase the lifespan of these seals. If you are storing O-rings on a shelf, it is recommended to make sure they are not stored under any sort of significant compression. Some materials can last up to 20 years on the shelf. Be sure to ask for shelf life information if you expect to keep these on a shelf for an extended period of time as most elastomers have a recommended shelf life.